A strong spring wind rattles the metal, corrugated barn on the Cory Family Farm where inside, a few dozen sheep cluster next to a wall.
Across the barn on the opposite wall, shearers are at work quickly removing a year’s worth of shaggy, white fleeces from ewes and rams. The shorn sheep emerge, looking sleeker and slightly pink, and squeeze back into the flock.
By the end of the day, over 100 sheep at this organic farm near Elkhart, Iowa, will have lost 7 to 8 pounds of wool.
Yet the fiber brings in little money.
“We'll get just a few cents a pound,” said Mary Cory.
Shearing is essential for the health of the sheep. Removing thick, dirty wool prevents them from overheating in the summer and reduces the risk of skin diseases and parasites. It also makes it much easier for lambs to reach their mother’s udder.
When Tom Cory first started raising sheep in the early 1960s, the wool brought in enough money to pay for winter feed.
“Today, I can’t even pay for half of their shearing,” he said, despite receiving a federal wool subsidy. “That’s how it’s changed.”
The couple, like most producers in the Midwest, raise sheep for meat – not high-quality fiber. But as prices for medium and coarse wools have dropped in recent years, many feel like this byproduct is a burden rather than a bonus — with some dumping wool in ditches or burning it just to get rid of it.
The prices are connected with global forces far from farms in middle America.
“We’re at a huge slowdown for wool processing worldwide,” said Jaelyn Whaley, a sheep field specialist with South Dakota State University Extension. “But here in the U.S. a lot of it has to do with the fact that our coarser wools were what got exported, and our export markets still have not really recovered.”
The export pipeline constricted after China – the biggest importer of American wool since the early 2000s – added 10% and then 25% tariffs during the trade war.
Soon after, the COVID-19 pandemic shut down wool processors and disrupted supply chains. Shipping costs increased, and office workers, already dressing more casually compared to decades past, were no longer buying wool suits and coats as they worked remotely.
But no matter the market, sheep kept growing wool, resulting in a global oversupply that continues to tug down prices.
“We're in a really, I think, volatile place right now,” Whaley said. “ ... because our numbers are dropping, and we’re having a hard time keeping people in the industry.”
The number of large commercial wool buyers also has decreased. Now Groenewold Fur & Wool Company, based in Illinois, is the only large wool buyer left following Mid-States Wool Co-Op closure last year.
Still, Whaley is optimistic as sheep producers pivot to new breeds and new markets.
“We just have to be innovative and make those changes that are profitable,” she said.
Raising sheep without the wool
For some, producing sheep at a profit means switching to “hair” sheep.
Breeds like Dorpers and Katahdins naturally shed in the spring, which cuts out the need for shearing. They also have higher heat tolerance and resistance to parasites compared to many wool sheep breeds.
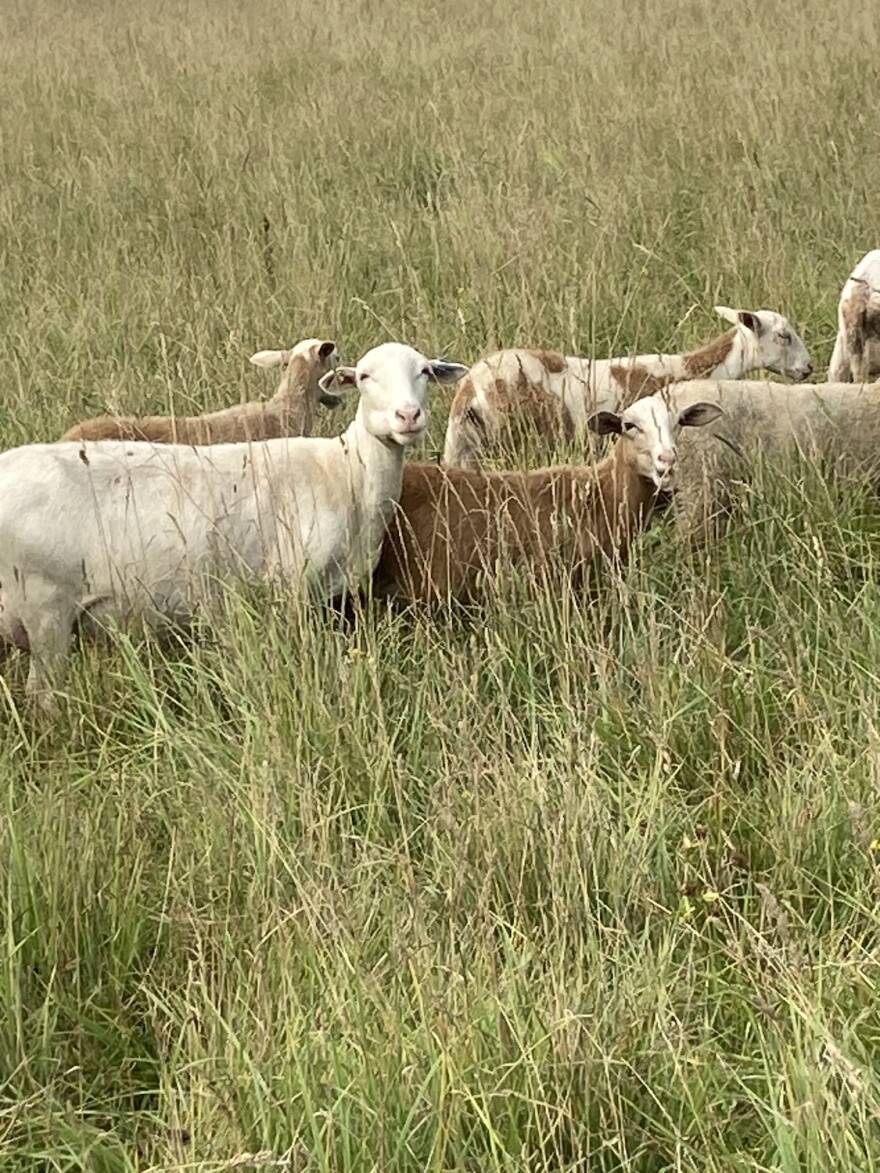
Texas, the state with the most sheep in the U.S., has more hair sheep than wool sheep today, and Whaley said the trend is catching on further north.
“In Iowa and the Midwest and even eastern South Dakota, we are seeing a bigger shift in people going to the hair sheep,” said Whaley.
It’s a shift the Cory family is making, although gradually.
Tom and Mary Cory bought a small flock of Katahdins for one of their sons to raise when he gets out of the Army. They say hair sheep make sense for a lot of producers because they don’t need to be sheared, and as Mary Cory points out, they also have good mothering skills and natural instincts.
“Some of them maybe don’t grow as fast as our wool sheep. So, for some people that would be a detriment,” she said.
To produce larger sheep that don’t need as much shearing, Tom has started cross-breeding some of the Katahdins and wool sheep.
But Ron Kilstrom, one of their shearers helping on the Cory Family Farm and a sheep producer himself, is unlikely to make the switch.
“Having been in the wool business and shearing business for over 40 years, it disturbs me,” said Kilstrom, laughing. “It’s like a dog that doesn’t bark.”
New uses for medium and coarse wool
Wendy Johnson, a regenerative, organic farmer in northern Iowa, has found a new use for her medium-grade wool.
She pulls thick, spongy batting out of her closet; it’s creamy white and lightly speckled.
“This is what fills the pillows, and it’s just such a nice fiber,” said Johnson.
She points out that wool is thermoregulating – meaning it can keep people comfortable in hot or cold conditions as bedding or clothing. It’s breathable, moisture-wicking, hypoallergenic and antimicrobial, which reduces odors, and when felted, wool can repel water.
Walking between recently planted nut trees and a fenceline, a heavy fog hangs above the pasture where her flock of Isle-de-France sheep graze.
“We could go to hair sheep, but not only do I love wool, but I also want to share the importance of wool as a fiber in the United States,” said Johnson. “We raise this incredible animal on grass and sunshine and rain and soil alone, and they just keep growing this renewable fiber that has all of these attributes.”

In south, central Nebraska Megan Landes-Murphy is using wool from her sheep and other producers to make a natural garden fertilizer.
Mixed into the soil or applied like mulch, the wool pellets provide plants with nitrogen and act like tiny sponges, absorbing excess moisture and releasing it back into dry soil.
Landes-Murphy founded Kestrel Ridge Pellet Company in 2022 and now buys around 30,000 pounds of wool each year from a local shearing crew and turns it into pellets. She’s excited to be helping other sheep producers.
“I’ve heard of them just burying or burning their wool just to get rid of it, because they feel like that’s the only option they have,” she said. “So, I think wool pellets are a great outlet for this underutilized wool, and then it’s also beneficial for plant enthusiasts and gardeners, alike.”
University of Vermont researchers found wool pellets perform as well as commercial fertilizer in organic vegetable production.
Producing finer wool
Regina Frahm and her family in central Iowa raise a fine wool sheep breed called Cormo, alongside a commercial meat flock. She said the Cormo fleeces have a waiting list from hand spinners and generate enough revenue to cover the costs of raising them. But they’ve found a way to tap into the fiber arts market – spinning, knitting, weaving – with the commercial flock’s wool, as well.
“For any breed of sheep, if you’re wanting the wool to be more profitable, it needs to be clean,” said Frahm.
They put coats on the Cormos to protect their fleeces from mud and hay. Other small changes on the farm, like spacing out bale feeders, keep both breeds cleaner. On shearing day, Frahm said they also spend a lot of time removing stains, burs and other contaminants from the fleeces.
Paired with better nutrition and breeding, Frahm said the commercial flock's wool has improved and is now a medium-wool.
“It’s great for more utilitarian yarns, like socks, hats, mittens, things like that. So, we actually sell a lot of those fleeces to hand spinners, as well. A lot of people weave with it, too,” said Frahm.
The wool that isn’t sold as fleeces goes to small and medium-sized woolen mills where it’s cleaned and turned into roving or yarn. Frahm then sells the products to knitters and other handcrafters.
She said there are more small and medium-sized woolen mills in the Midwest now, compared to a few decades ago. There are also more producers raising small flocks specifically for the fiber arts, which had a renewed interest during the pandemic.
Jaelyn Whaley with South Dakota State University Extension said many of these handcrafters want something local.
“A lot of them like to know the story of where that wool came from. But that takes a lot of work on the producer end to market that product,” she said.
Whaley sees possibilities for sheep producers who are willing to try a variety of new things.
“There is a lot of opportunity for the sheep industry,” she said. “We just have to stop thinking, ‘Well, that’s always the way we’ve done it.”
This story was produced in partnership with Harvest Public Media, a collaboration of public media newsrooms in the Midwest. It reports on food systems, agriculture and rural issues.